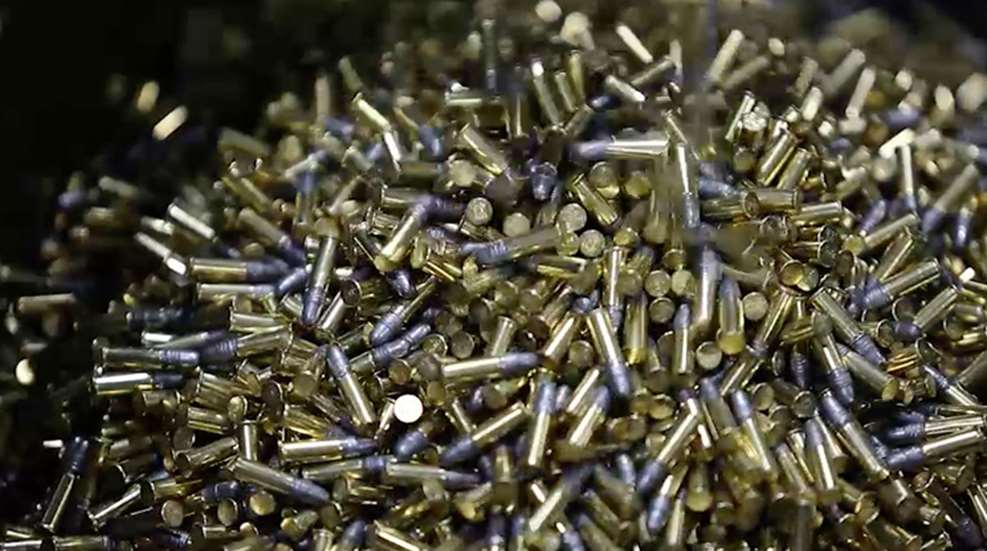
This article was first published in Sept. 2010. The author is former NRA Publications Technical Editor.
Images copyright American Rifleman
In the subconscious mind of most shooters, the .22 Short, Long and Long Rifle rimfire cartridges form part of the bedrock of shooting sports. Their ubiquitous availability, affordable price, consistent quality and wide product range are taken for granted. Few shooters stop to consider the many difficulties inherent in the design and manufacture of these cartridges.
If you set out to design a self-contained cartridge that is difficult to make and suffers from numerous design shortcomings, it would be the humble .22 Short, Long and Long Rifle (.22 rimfire).
Design Shortcomings
On a good day, the ignition potential of the .22 rimfire priming system is weak. Because there is no anvil, the lead styphnate rimfire priming compound requires the addition of ground glass as a frictioning agent. Ground glass is not "bore friendly," but without it, .22 rimfire priming will not function. And, to date, no lead-free priming compounds suitable for .22 rimfire have been found.
Ignition begins on the side of the case where the rim is crushed by the firing pin; there is no flash hole to focus the ignition gasses into the center of the powder charge. Failure to press the priming compound reliably and evenly inside the annular rim cavity can lead to misfires and high variations in muzzle velocity.
It is important to remember that the .22 Short and Long Rifle cartridges were originally designed for and loaded with easily ignited black powder. However, smokeless propellants have dramatically different ignition requirements and burning characteristics. Propellant makers soon found that the .22 rimfire design was not friendly to early smokeless propellants. They struggled for decades to find suitable smokeless propellants and the search continues to this day.
Essentially, the .22 rimfire requires unique smokeless propellants with a high energy content that are easily ignited and burn progressively. Limited case capacity dictates a dense powder with a small flake or ball configuration. Propellants with large flakes, sticks or coarse grains cannot be used as they will not drop uniformly through the holes in .22 rimfire plate-loading machines.
To facilitate ignition, .22 rimfire bullets must be heavily crimped into the case mouth to increase shot-start forces. Of necessity, this deforms the bullet. However, even on a good day, only about half of the propellant in a .22 rimfire cartridge burns completely.
The weak case head is the Achilles heel of the .22 rimfire cartridge. For this reason, Maximum Average Pressures (MAP) of .22 rimfire ammunition must be kept below 24,000 psi. Rimfire cases must have enough spring-back to assure consistent extraction in blowback-operated semi-automatic guns, yet remain soft enough to prevent splitting. This is a narrow margin that also eliminates steel as a .22 rimfire cartridge case material. Design parameters require all rimfire cartridge cases to be rimmed. Necked rimfire cases require several additional production steps which adds considerably to their cost. Rimfire cartridge cases cannot be reloaded.
All .22 rimfire bullets tread a fine line between function and accuracy. The bearing surface of .22 rimfire bullets is the same diameter as the outside surface of the cartridge case. This makes lubrication of such bullets difficult as the case-diameter bullets must be lubricated on the outside where it may be wiped off or contaminated. Lubricants for lead, center-fire bullets are unsuitable for rimfire ammunition, and, unfortunately, copper-plating serves no ballistic purpose, does not eliminate the need for lubrication, adds cost and damages the bullets.
Case-diameter bullets also limit bullet shape, weight, balance and bearing surface. Another significant problem is that .22 rimfire bullets have an undersized, cupped base that the propellant gases must expand reliably and evenly into the rifling grooves for proper sealing and stabilization.
Headaches of .22 Rimfire Production
Centrifugal force is used to push the priming compound into the hollow rim of the cartridge case. This is accomplished by dropping a wet pellet of priming compound into the bottom of the cartridge case, inserting a closely fitting steel pin, then using the pin to spin the case at speeds of approximately 10,000 rpm for a few seconds. This is a tenuous process at best and frequently fails to completely fill the rim with priming compound.
Preparing the small, wet primer pellet and inserting it in the cartridge case is hazardous hand work—part art and part training. The moisture content of the priming compound must be carefully controlled within narrow limits, otherwise the mixture will not work at all. The ground glass in the priming compound increases wear on the steel spinner pins and excessive smearing of the priming compound up the case sidewalls (a common problem) can adversely affect ignition and interior ballistics.
Ammunition makers also struggle continuously to find suitable rimfire powders. The ideal .22 rimfire propellant must be competitively priced and compatible with plate-loading systems. It must have a high energy content, ignite easily and burn progressively while leaving a minimum of unburned propellant. Very few propellant powders meet these requirements.
Due to the weak ignition, powder residue from partially burned and unburned powder are constant problems—just ask any indoor shooting-range operator. The high ballistic performance required by many modern .22 Long Rifle loads places severe interior ballistic requirements on propellants. On the other hand, low MAPs can cause uneven expansion of the lips of the cup on the bullet's base and poor accuracy. In some instances, high MAPs can blow the lips of the cup base completely out.
In order to obtain the high muzzle velocities advertised for many .22 Long Rifle loads, MAP limits must be pushed to levels that leave little margin for error given the weak case head. Also, the proper case hardness gradient must be maintained to prevent extraction and/or ejection problems in spite of variations in brass strip and tooling.
Rimfire .22 ammunition makers fight a constant battle with bullet lubrication. It is ironic that such a cheap cartridge requires highly specialized, micro-crystalline, synthetic-base waxes for lubrication and costly systems for application. Often, what works today does not work tomorrow due to minor variations in temperature, humidity, bullet hardness, propellant variations, etc.
Bullet hardness (antimony content) can be a particularly difficult problem as small variations can result in lead buildup of rifle bores and inaccuracy. Rough handling of .22 rimfire bullets on the factory floor can easily have an adverse effect on accuracy.
Crimping the .22 LR bullet into the case mouth properly remains a constant problem. Too heavy a crimp may push MAPs over the limit, adversely affect accuracy and cause leading. Too light a crimp may result in erratic breech pressures, high variations in muzzle velocity, excess unburned propellant and malfunctions in semi-automatic firearms. As if this were not enough, the driving knives on the crimping operation mangle the bullet.
Overview of the Impossible
We have seen that the inherent characteristics of the .22 LR rimfire cartridge are its own worst enemy and the leading cause of its manufacturing difficulties. However, before we condemn its design, we must remember that the .22 LR rimfire cartridge is a product of the technology and art of the 19th century. With the benefit of today's technology, ammunition makers produce safe, reliable, low cost .22 LR cartridges of average quality in mind-numbing quantities. However, they cannot produce a match load on demand. That is the art.
On the other hand, the .22 LR is nothing if not adaptable. Its repertoire includes instruction, training, practice, qualification, informal competition, formal competition, plinking, pest elimination, small game hunting and even personal defense. Few other cartridges are this versatile. And, that is why the .22 LR rimfire cartridge remains a bedrock of the shooting sports.