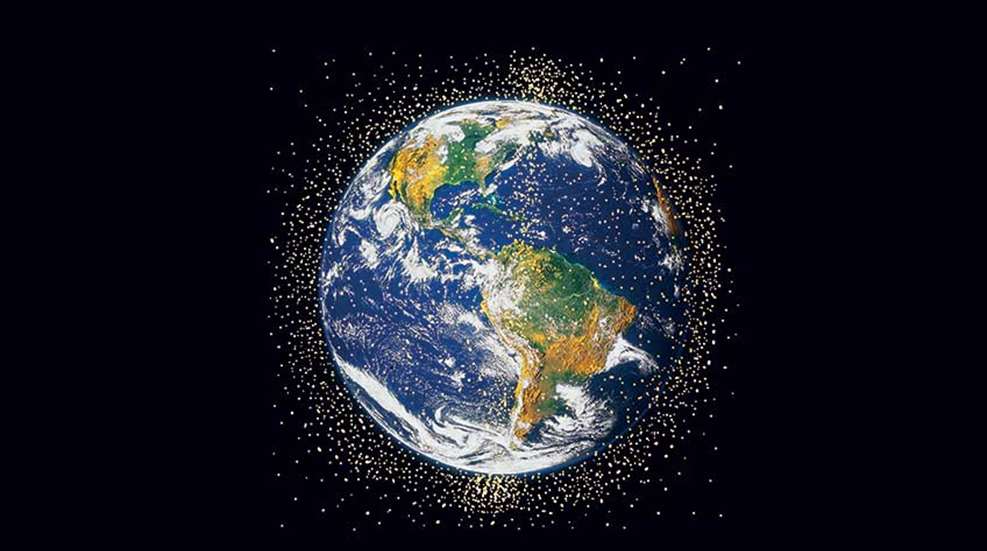
This article, "The Guns of NASA," appeared originally in the August 2003 issue of American Rifleman. To subscribe to the magazine, visit the NRA membership page here and select American Rifleman as your member magazine. Photos courtesy of NASA. Written by: William L. Ross Sr., Donald Henderson and Claire G. Meador, Technical Editor, NASA Johnson Space Center White Sands Test Facility.
In the desert foothills where the six-guns and rifles of Pat Garrett, Billy the Kid and Geronimo once barked, the big guns of NASA now thunder. Those figures of American history would have been awed at the size, power and purpose of NASA’s light-gas guns that send projectiles downrange at the speed of shooting stars.
At a remote location northeast of Las Cruces, N.M., the rich legacy of the Wild West commingles with the modern Space Age at NASA Johnson Space Center (JSC) White Sands Test Facility (WSTF) where a select group of technicians, engineers and scientists support Space Shuttle and International Space Station (ISS) missions by testing all materials used in the Space Program. Their primary responsibility is to promote and ensure Mission safety, of which the guns of NASA play a critical role.

For millions of years, Earth has been bombarded from outer space by meteoroids. An orbiting layer of man-made debris, composed of spent rocket fragments, exploded satellites and other space mission bits and pieces now join the naturally occurring meteoroids. Those objects travel at hypervelocity speeds—by definition in excess of 6,600 f.p.s.—and are a significant threat to spacecraft during launch, orbit and re-entry operations.
Space debris impacts are a real danger to astronauts doing extra-vehicular maneuvers and to high-pressure vessels and toxic aerospace materials carried aboard spacecraft. Traditionally, astronauts have faced these life- and mission-threatening dangers every time they went into space. Their defenses are much better now, with improved shielding and ballistic-quality windows that protect them from impacts caused by the smaller pieces of space debris.
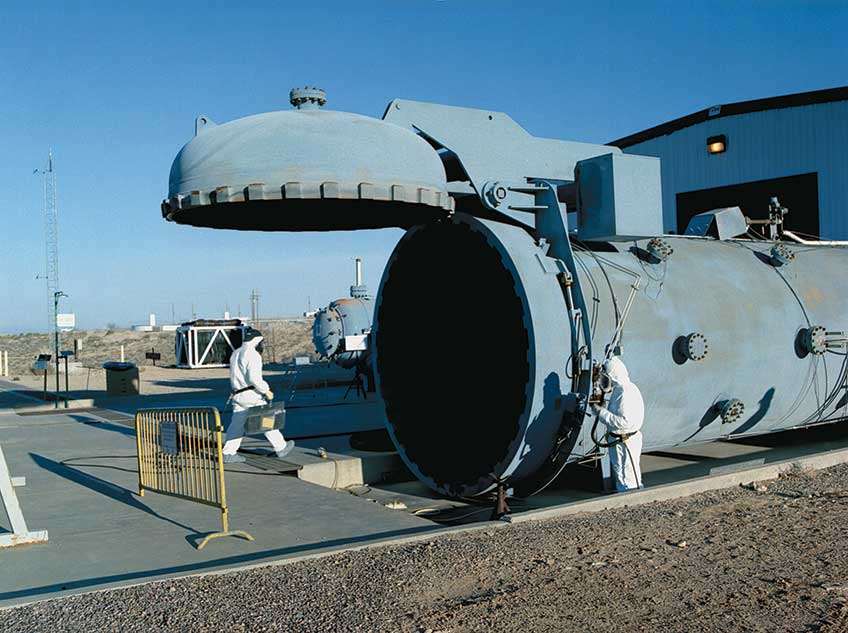
The Hypervelocity Group at WSTF works in close partnership with the JSC Hypervelocity Impact Technology Facility (HITF) in Houston. HITF determines the risk posed by space debris and designs spacecraft shields based on probability of impact and spacecraft geometry. HITF builds and sends target shields to WSTF for ballistic-limit verification testing and then analyzes the results. Other spacecraft materials and components are also targeted, as well as toxic and explosive cargo including fuel (up to 5-lb. TNT equivalent).
The WSTF Hypervelocity Impact (HVI) Testing Program assesses candidate shield materials using two-stage light-gas guns (LGG). These guns shoot projectiles at hypervelocities up to 24,000 f.p.s., roughly six times faster than the fastest rifle bullet, and mimic the impact of real space debris traveling at even higher speeds.
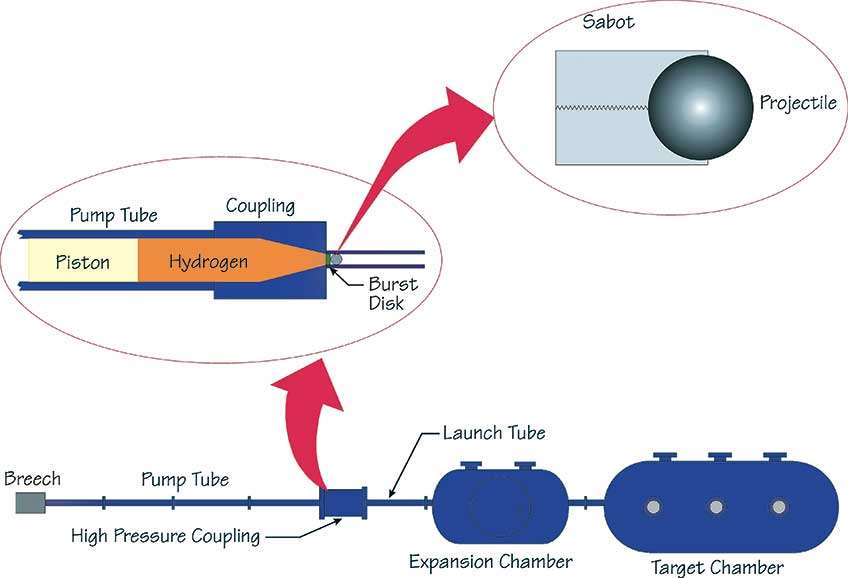
This schematic diagram illustrates how NASA’s 1” light gas gun hurls tiny projectiles toward their target. The gun’s breech contains the first-stage charge of smokeless powder, set off by an electronic igniter, and upon exploding provides the rapidly expanding gas that drives the piston forward. The high-strength, heavy-wall pump tube contains the precision-machined plastic piston assembly that rapidly compresses the light gas column and provides the second-stage firing power. The taper-bored, high-pressure coupling halts the propelled piston at the end of its travel down the pump tube. In the HP section, rapid internal pressurization is followed by an extremely high level of impact caused by the halted piston. Upon petal-valve rupture, the sabot is launched—propelled by the rapidly expanding light gas—down the barrel into the expansion tank. The expansion tank allows collection and dissipation of second-stage, high-pressure light gas and permits the controlled separation of the sabot/projectile assembly. It is equipped with optical ports for in-flight photography of projectiles. The target tank is designed to contain resultant second-stage light gas and the eruption of shrapnel and debris from the impacted target. It, too, is equipped with optical ports.
The main LGG facility at WSTF houses 1”, .50- and .17-cal. guns. Because of the hazardous nature of the testing, the facility was built in a remote location, and the LGGs are remotely operated from underground control bunkers. Television cameras constantly monitor the entire area. Access warning lights, signs and a remotely operated road gate control all possible area entry. Safety or warning announcements are broadcast before and after each shot. For non-hazardous testing, smaller .07- and .17-cal. guns are operated within another controlled-access laboratory.
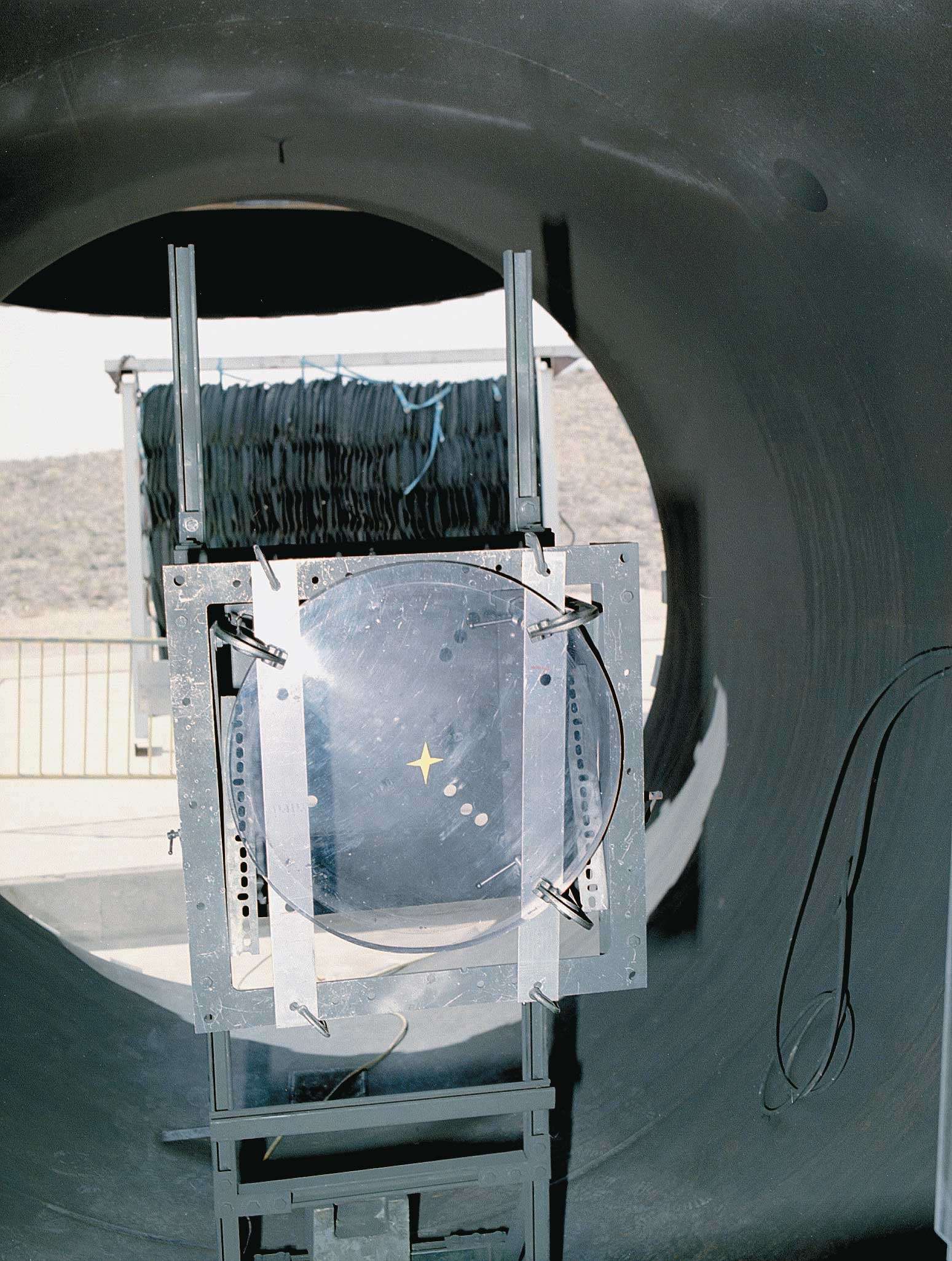
The two-stage LGG uses conventional smokeless gunpowder as its first stage. The second-stage propellant is a highly compressible light gas such as hydrogen. Since light gases have very low molecular weights, they can be more rapidly compressed to the high pressure levels needed to efficiently launch projectiles at hypervelocity speeds—usually from 8,000 to 24,000 f.p.s.
Depending on the gun and velocity required, smokeless powder charges range from 21 to 27,800 grs. (about 4 lbs.). The smokeless charge propels a cylindrical polyethylene (plastic) piston at 2,500 f.p.s. down the “pump tube,” compressing the hydrogen gas. The piston enters the reduced taper bore of the high-pressure (HP) section and deforms in a rapid, energy-absorbing stop. A stainless steel petal-valve diaphragm retains the gas until it bursts under pressure, and the highly compressed (over 100,000 p.s.i.) hydrogen rapidly expands, accelerating the launch package down the barrel with little loss of energy.
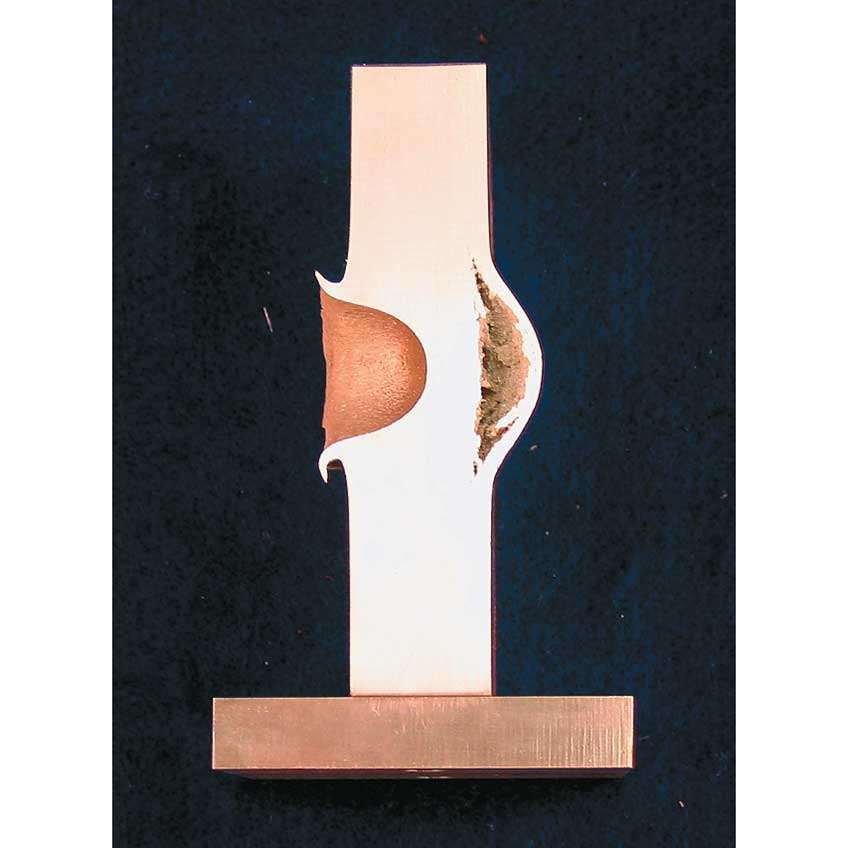
The hydrogen dissipates through the muzzle into an expansion tank. A stripper plate separates the launch package (sabot and projectile) while in free flight. The projectile then enters the evacuated target tank where it impacts the target.
The projectile is photographed with high-speed cameras and flash X-rays just before impact. At times, the impacts are photographed to characterize the debris cloud. Three types of high-speed cameras are used. Cinema cameras run at 10,000 frames per second; 35 mm infrared cameras are capable of 2 million, and the digital cameras are capable of 100 million frames per second.
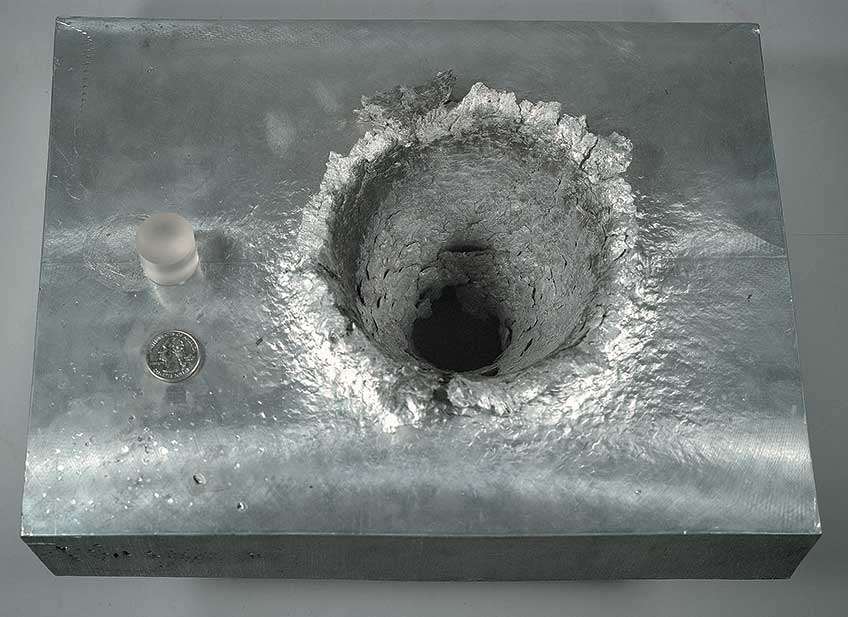
Laser intervalometers measure projectile velocity. The time difference between interruption of laser beams by the projectile yields an extremely accurate calculation of its velocity—in the case of the 1” LGG, 23,000 f.p.s. in just 22 ft. of barrel. In addition, high-speed data acquisition systems—using light detectors, strain gauges, pressure transducers, accelerometers and thermocouples—provide reliable diagnostics.
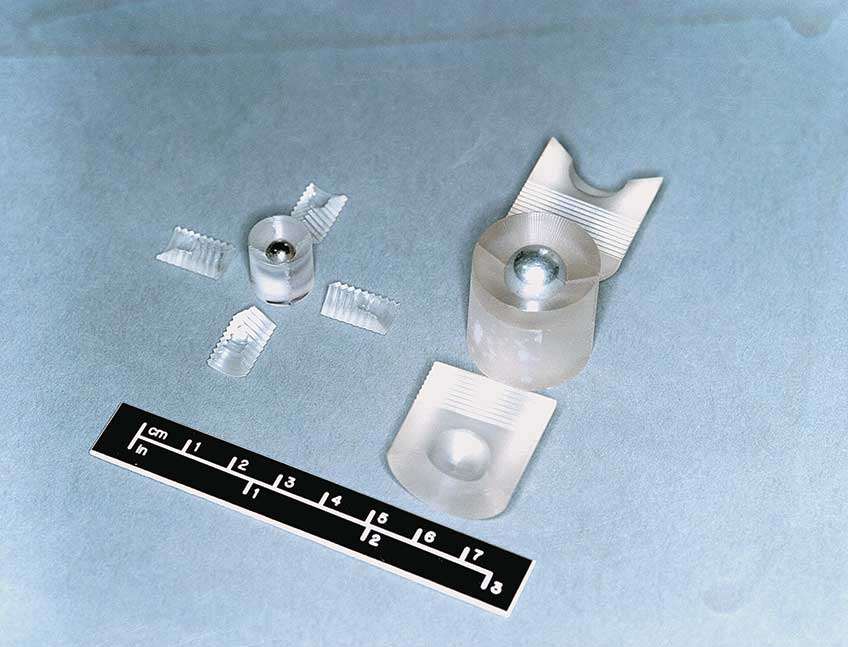
The barrel—a long, high-strength section of steel with a precision-honed smooth bore—allows for controlled acceleration of the propelled sabot/projectile assembly into the downstream expansion tank. A horizontal honing machine uses computer-controlled depth of cut, automatic fluid feed and a single-spindle 14-stroke reciprocating/rotating-stone honing tool with various grit sizes. Before honing a new barrel, a plastic slug is fired to knock off the bore’s rough edges. Initial honing establishes the original LGG bore size. Subsequent honing cleans the bore and establishes the new bore size for the next sabot.
LGG alignment is checked before every shot. A pedestal-mounted surveyor transit sights down the bore’s centerline from the open end of the LGG’s powder chamber (breech). The gun is bore-sighted, focusing the transit on various alignment plugs located at both ends of the pump tube and the barrel, and the HP section. LGG alignment is further verified by sighting on the stripper plate orifice in the expansion tank and finally on the pre-marked target itself. Accuracy for any of the WSTF LGG shots are normally within one projectile diameter of the marked point of impact on the target.
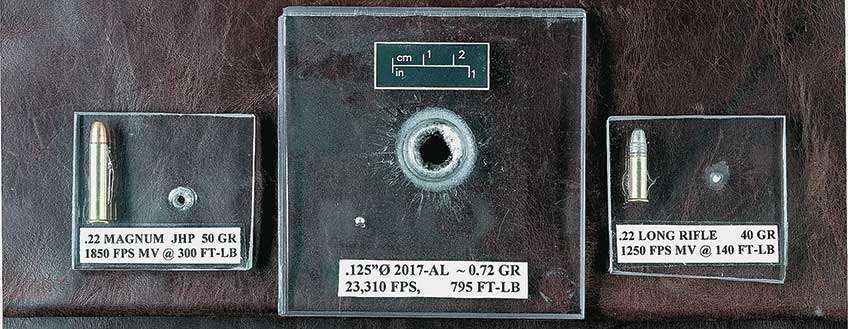
The projectile/sabot launch package is carefully loaded into the entry end of the barrel. The petal valve and ring seal are inserted behind it, and the gun barrel assembly and HP section are clamped together with hydraulic collars. At the entrance end of the pump tube, a freezer-stored, ultrahigh-density 12-lb. polyethylene piston is inserted. The front face of the piston is a hollow cone that forms a gas seal as it compresses the hydrogen at a speed of about 2,500 f.p.s. The back end of the piston uses an O-ring to seal the expanding gases from the smokeless powder charge.
Once the LGG is reassembled, a smokeless powder charge is inserted into the breech. A typical powder charge is about 18,500 grs. (2.6 lbs.) of IMR 4831 for the 1” LGG. Maximum charges use 4.1 lbs. An electrically activated standard Mark 27 torpedo igniter is contained in the center of the powder charge. The downstream barrel section, expansion tank and target tank are maintained at near vacuum in readiness for firing.
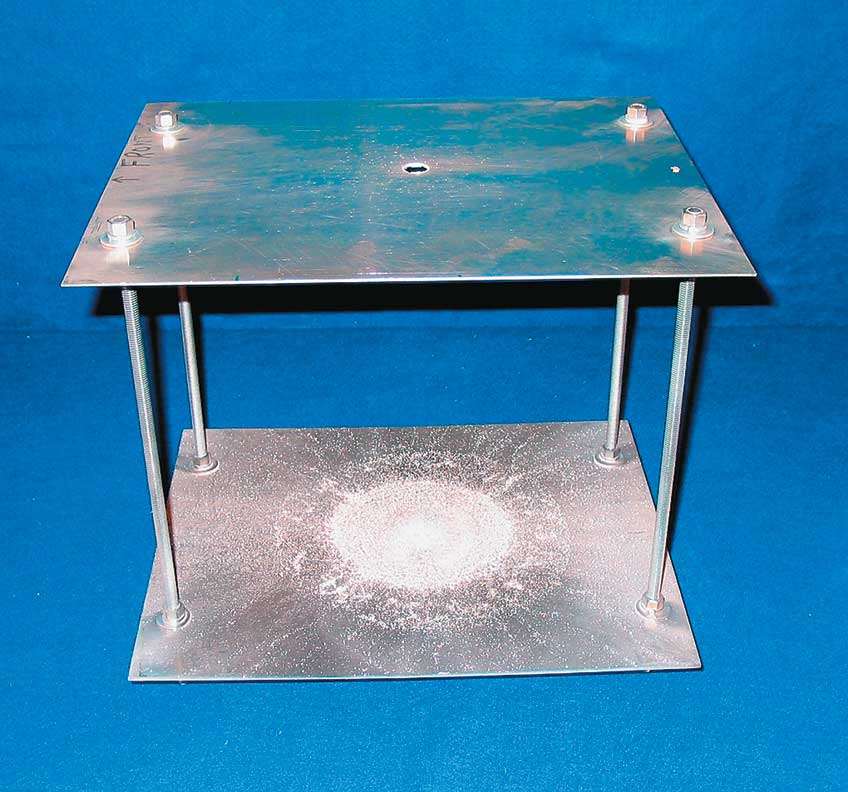
Firing is performed from one of the underground control bunkers. Area TV surveillance monitors are checked to ensure that the area is secure, warning announcements are made and the bunker blast doors are secured to provide overpressure protection. The area warning lights are switched to red. The pump tube is remotely backfilled with hydrogen to 50 p.s.i.g. The firing circuit is turned on, and the X-ray system and high-speed cameras are activated. After a countdown, the “FIRE” button is pressed.
The LGG, as with any other powder-charged gun, recoils upon firing. To accommodate that, the entire gun assembly is held within either anchored sleeves or sliding anchor assemblies, which allows the gun to move both forward and back. When the powder charge ignites, the normal recoil is counteracted when the forward-moving piston slams into the reduced taper HP section.
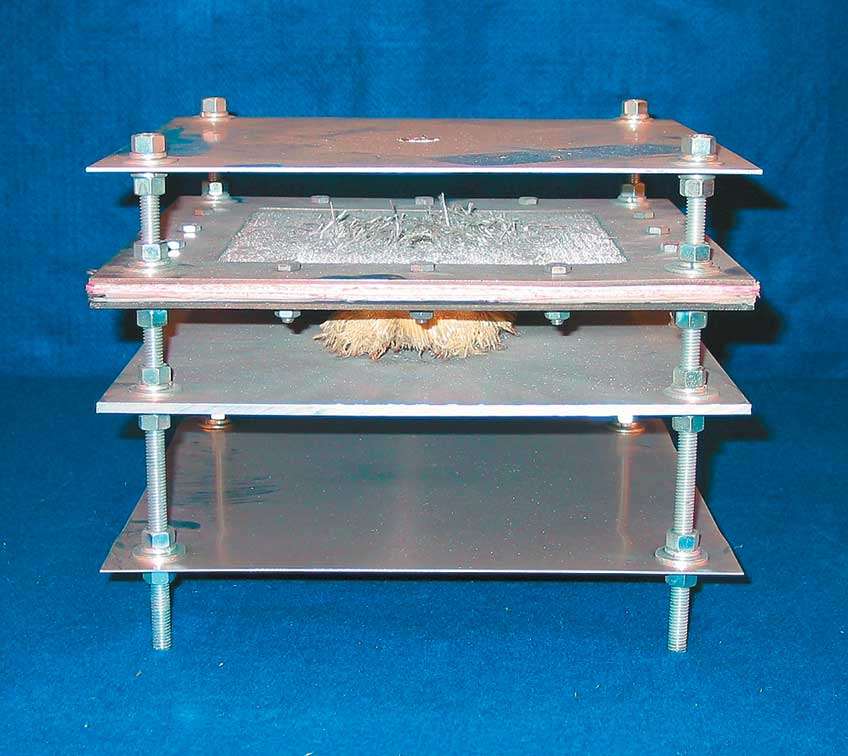
The muzzle end of the barrel is sleeved into the expansion tank at the entry flange orifice with O-ring seals that accommodate movement in either direction. That linear recoil arrangement essentially isolates the anchored expansion and target tanks from any effects of recoil that could affect accuracy.
The basic designs of WSTF LGGs originate from the 1940s and 1950s, with improvements and updates made through the years. Most of the gun parts are made from high-strength, low-alloy steels, such as AISI 4340, with a minimum design yield strength of 140,000 p.s.i. Recently, the need for higher-strength materials was established to provide added safety, extended life and increased gun performance.
In 2001, the Hypervelocity Group purchased some highly engineered Grade C250 maraging steel for a new .50-cal. HP section. It was supplied as a fully annealed, rough-turned custom forging. The critical taper bore was precision-machined using electron-discharge machining. After machining, the part was then heat treated to achieve its final properties. Test results indicate a yield strength of 285,000 p.s.i., twice the minimum design yield strength required for conventional gun steels used at WSTF.
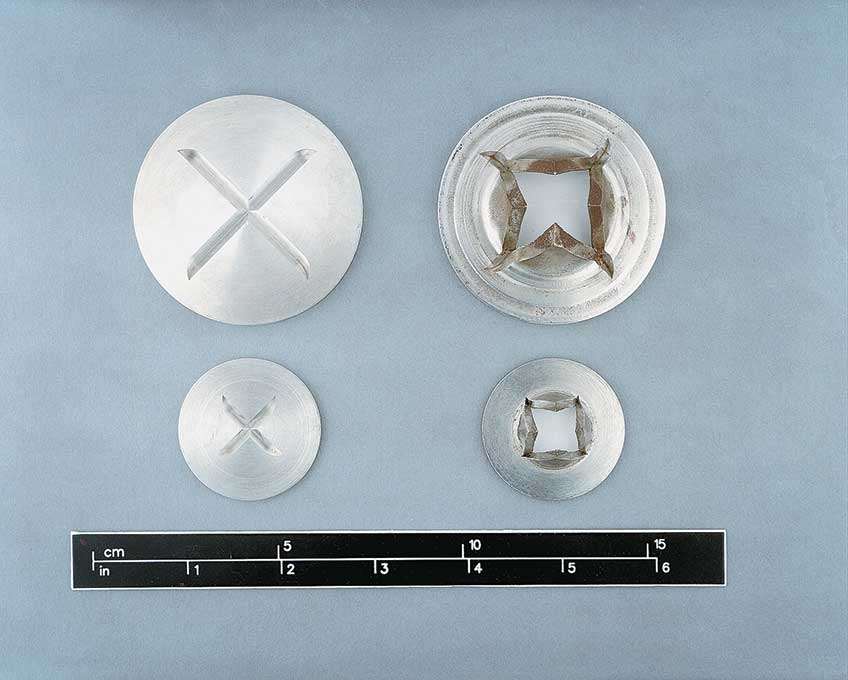
All gun components are thoroughly inspected and verified using ultrasonic testing, magnetic particle testing, X-ray, chemical analysis, Charpy V-notch, and tensile and hardness testing. A rigorous final dimensional inspection is also performed in strict accordance with NASA design drawings.
HVI testing at WSTF has contributed significantly to the design and evaluation of materials and shield configurations for the ISS, Space Shuttle, Extravehicular Mobility Unit (EMU), Long Duration Exposure Facility, Russian Space Station Mir, the X-38 and the ISS-proposed Crew Return Vehicle. Because of the program’s success, the future of Hypervelocity Impact Testing will continue to include evaluation of new materials and concepts for the space program.
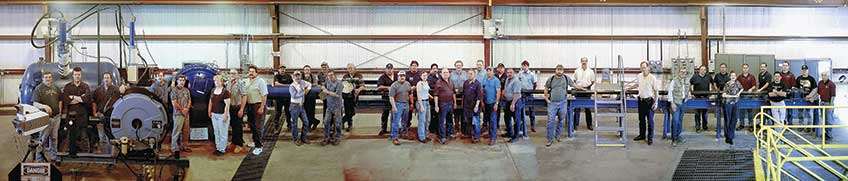
NASA is currently evaluating the feasibility of manned missions to Mars. Although debris generated by man is not a problem once we are away from Earth, the threat of meteoroids with unknown velocities presents us with new challenges. Some estimates of velocities in our solar system are up to 230,000 f.p.s. Deep-space debris may travel even faster, up to approximately 787,000 f.p.s. New technology may emerge to enable scientists to more accurately predict the terminal ballistics of such super-high-velocity debris.
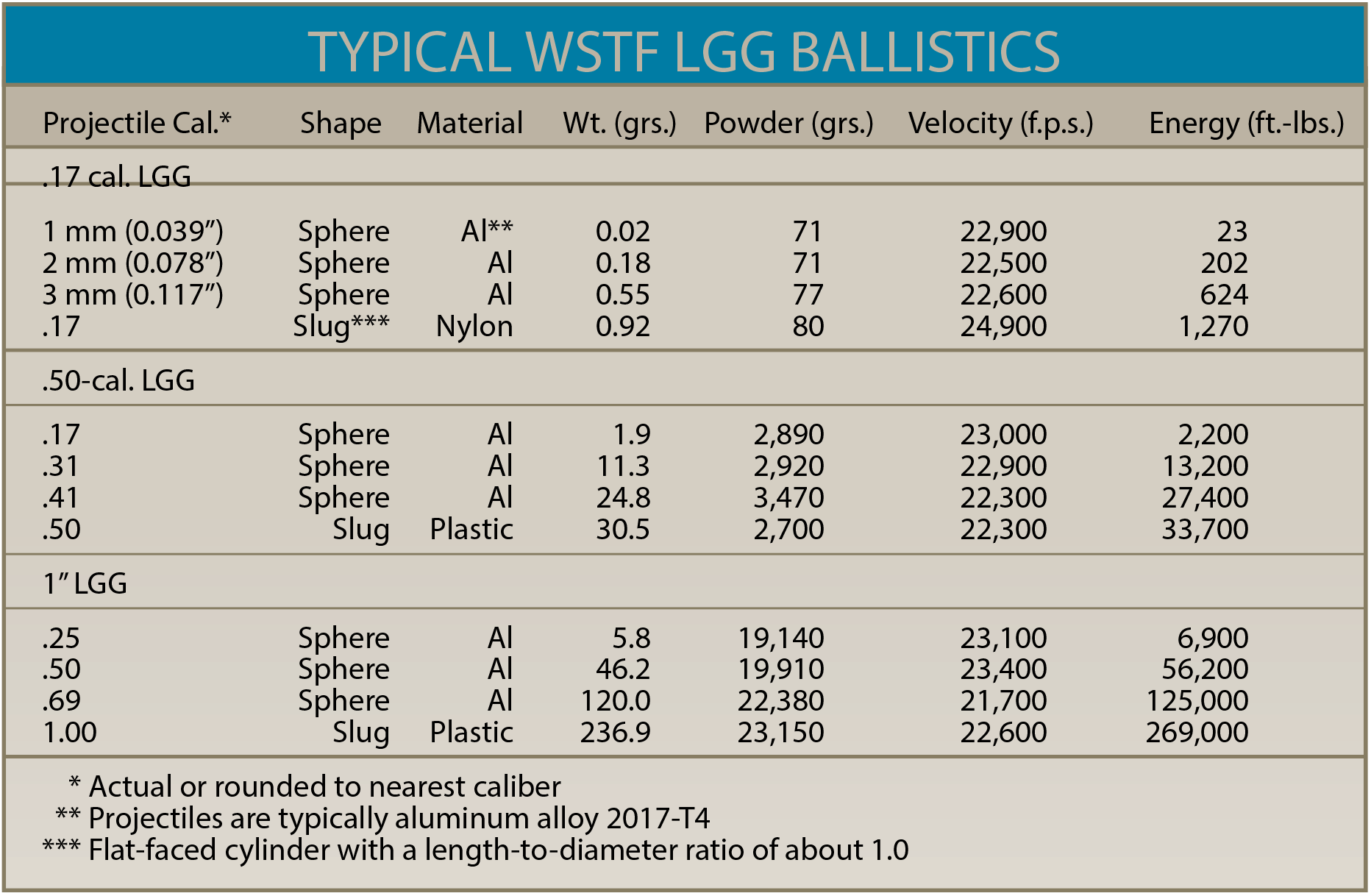