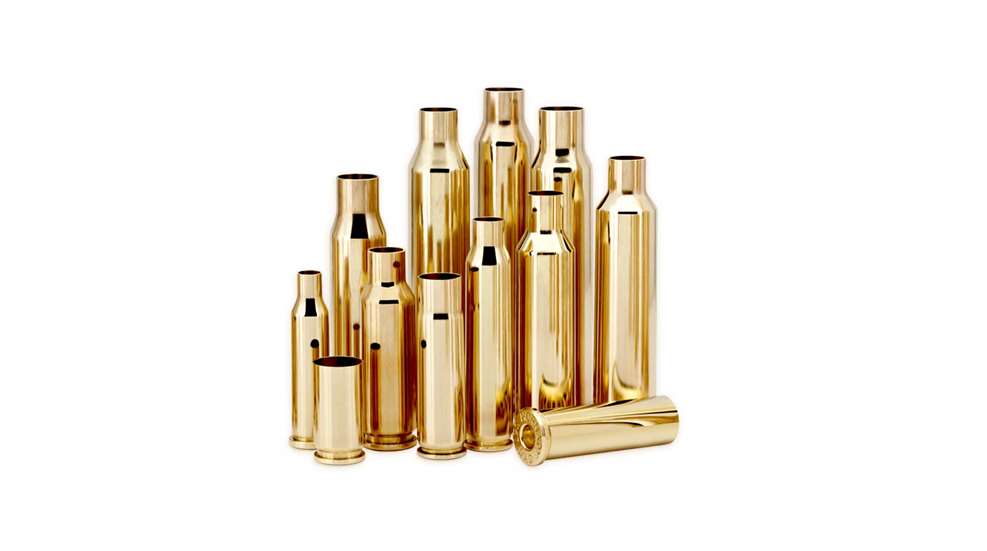
Technology for making steel cartridge cases was developed in Germany during World War I and was well-developed by the time World War II began in 1939. It is important to note here that Germany and Russia fought World War II almost exclusively using steel cartridge cases. The U.S. military lagged behind in steel cartridge case manufacturing but launched a crash program to develop them during World War II. This program was successful and steel-case small-caliber military ammunition was made in large quantities in the United States during the war. However, it was used mainly for training, qualification and practice and was never used overseas. After World War II, the U.S. military standardized brass cartridge cases, and the use of steel-cased ammunition was limited to large calibers.
Until recently, aluminum was not considered suitable for small-caliber centerfire cartridge cases due to a characteristic called “burnout” that completely destroyed the gun if the case head failed. This phenomenon was caused by high-temperature propellant gas igniting the aluminum metal as it escaped through the failure point. Modern alloys have eliminated this problem in handgun calibers and metal heads for shotshells. However, aluminum alloys remain unsuited to high-pressure rifle cartridge cases unless complex and expensive measures are taken to protect the metal from burnout.
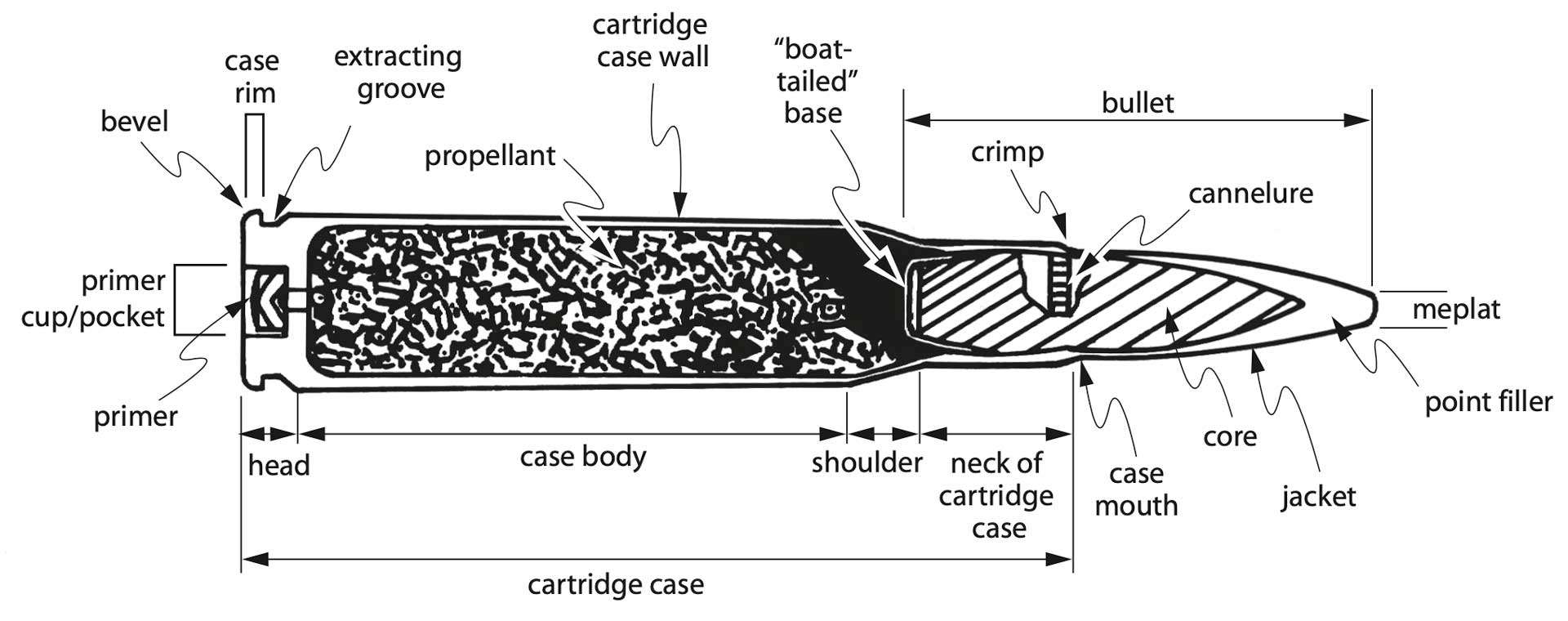
Centerfire rifle and handgun cartridge cases are normally made of metal. Over the years many types of metal alloy have been tried such as:
- brass (83 percent copper and 17 percent zinc)
- steel
- aluminum
- plastic
- hybrids combining two of the above.
Brass has proven to be the best choice for centerfire cartridge cases for the following reasons:
- It is readily available in large quantities.
- It is inexpensive.
- It is easy to draw and form.
- It can be hardened to make it springy.
- It can be annealed to make it soft.
- It requires no anti-corrosive coatings.
Experience and customer preference have made brass the metal of choice for sporting and competitive use. Brass is also the best metal for rimfire cartridge cases and for the metal head on shotshells.
Steel has proven popular for military use, particularly in Russia, China, Germany and France. While steel is cheap and widely available, manufacture of steel cartridge cases is more complex and expensive than brass. The main reason steel is popular for military ammunition is that it is readily available in wartime while brass (a “strategic” metal) is often not.
Plastic has been the holy grail of centerfire cartridge case materials. On initial consideration, plastic seems the perfect material for a cartridge case in that it is:
- inexpensive
- widely available in many different formulations
- moldable using well-known technology
- lightweight
- non-toxic
- waterproof
- non-corrosive.
Plastic has several major drawbacks for use in a centerfire cartridge case:
- It will not hold a primer securely.
- It will not meet bullet push or pull requirements.
- It does not spring back like metals.
- It lacks resistance to heat from hot barrels.
- It lacks strength to resist rough handling during feeding and extraction.
Never ones to give up on a good idea, ammunition manufacturers have invested considerable money and effort in developing plastics for ammunition applications since the early 1950s. Their efforts have not been in vain. Packaging is a successful application of plastics that immediately comes to mind in the form of boxes, trays and belt carriers.
Successful ballistic applications include shotshell hulls, shotshell wads, sabots, bullet tips and bullet coatings. Plastic centerfire cartridge cases have been tried, but thus far none has proven satisfactory. That may change, spurred by the promising development of hybrid cases in the late 1990s.
A hybrid cartridge case utilizes two or more different materials in its construction. The key is using materials in the application to which they are best suited. While this seems basic and simple, in practice it was not. Only recently have such efforts been successful. A modern, hybrid, center-fire cartridge case is made of a molded plastic front end and a metal (brass or steel) head. The metal head provides strength for extraction and holds the primer securely in position. A blow-through panel under the plastic case neck provides the requisite levels of bullet push and pull. The hybrid cartridge was a long time in coming, and only time will tell if it will be a commercial or military success.
The Cartridge Case
Case Types
There are several types of cartridge case head and rim configurations:
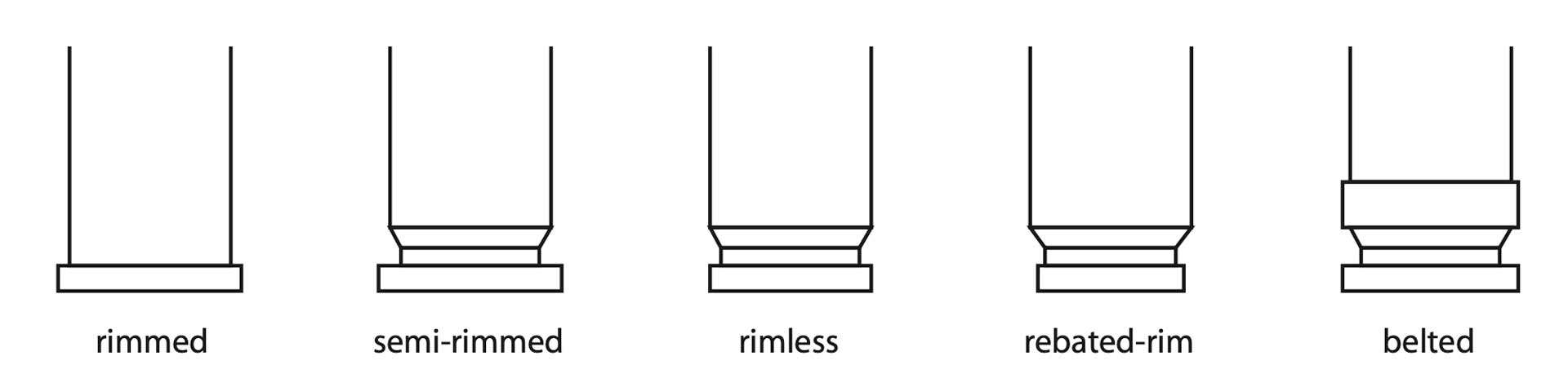
In addition, there are various cartridge case body configurations: straight, tapered and necked. These configurations are combined to describe a cartridge case. For example, rimless tapered (.30 Carbine), rimless necked (.270 Win.), belted necked (.300 Win. Mag.), rimmed necked (.30-30 Win.) and rimmed straight (.44 Mag.).
Brass cartridge cases are made in a series of steps:
- Draw—The cup is drawn, washed, annealed and trimmed. This step may be repeated up to four times to obtain the necessary length.
- Head form—The head is formed on the drawn tube by upsetting it with a punch and die set. This step also forms the headstamp and primer pocket.
- Head turn—The head is turned on an automatic lathe to form the rim. Taper and plug—The case neck, shoulder and body taper are formed and the case trimmed to length.
- Neck anneal—The neck is flame- or induction-annealed to soften it and relieve stress.
- Primer insert—The primer-insert machine punches the flash hole in the primer pocket, inserts a primer into the pocket and places lacquer sealer around the primer annulus. It also crimps the primer in place if required.
The Sporting Arms and Ammunition Manufacturers’ Institute (SAAMI) is an association of the nation’s leading manufacturers of firearms, ammunition and components. SAAMI was founded in 1926 at the request of the federal government and tasked with publishing recommended cartridge and chamber dimensions, as well as maximum pressures, for factory ammunition produced in the United States; the Commission Internationale Permanente des Armes a Feu Portative (CIP) does the same for European-made ammunition. These standards provide a benchmark for ammunition manufacturers, gun makers, gunsmiths and others in the firearm industry, and ensure that all ammunition of a given caliber is safe to fire in virtually any firearm chambered for it.
Shotshell Cases
A modern shotshell is a type of hybrid cartridge case. It consists of an extruded hull of high-density, polyethylene plastic, a base wad and a metal head with a pocket for a 209 battery cup primer. All shotshells are rimmed with a straight-sided case. Shotshells are offered in several gauges such as 10 , 12 , 16, 20, and 28 ga. as well as .410 bore. Case lengths vary from a maximum of 3 1⁄2" to 2". Many gauges are offered in several shell lengths. A short shotshell may be fired safely in a longer chamber, but a long shotshell must never be fired in a shorter chamber.
The extruded plastic tubes are often color-coded by gauge. For example, brown is utilized for 10 ga., red is used for 12 ga., purple for 16 ga. and yellow for 20 ga. At the mouth, the hull may be chamfered to provide a better crimp. Both six-fold and eight-fold crimps are in common use. The six-fold crimp is normally used on hunting shells and the eight-fold crimp is used on target loads for trap, skeet and sporting clays competition. Rifled slug shells are roll crimped.
For nearly 100 years, shotshell hulls were made of paper. The paper hulls were made by rolling a number of layers of glue and paper over a short steel mandrel, then cutting the long tube into short lengths. However, paper had little resistance to moisture. Contact with water caused it to swell to the point of being useless. When reliability was paramount in those days, all-brass shotshells were used, although they were much more expensive. Paper shells today are used almost exclusively for target shooting, although they are favored in some hunting areas for their environmentally friendly characteristics.
Inside every plastic or paper shotshell is a base wad. The base wad serves to control internal volume, reinforce the base area and help hold the primer in position. As a direct function of controlling volume, base wads are of different heights and configurations.
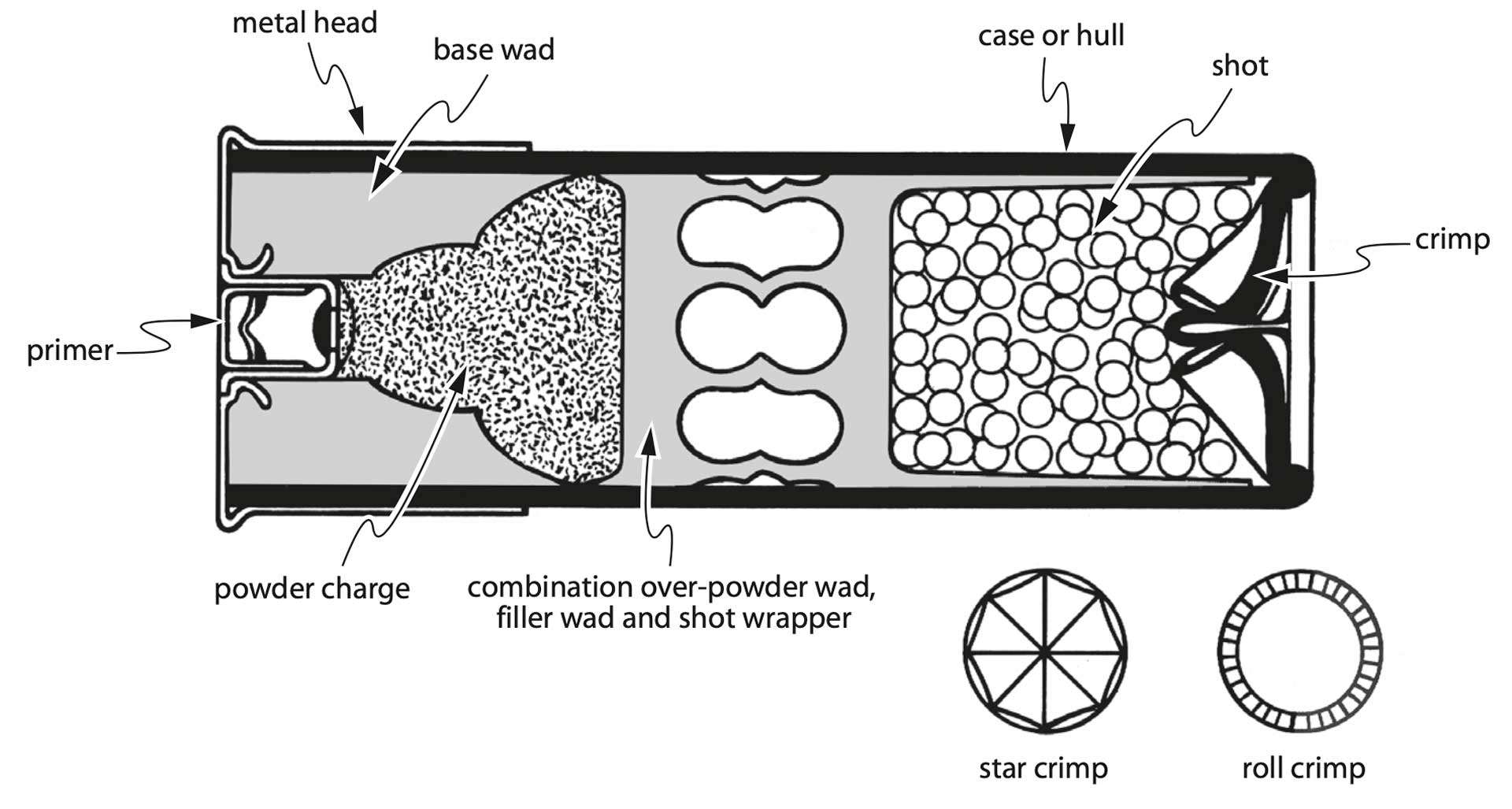
There are two types of base wad:
- Separate—This type of base wad is made separately and inserted into the tube prior to crimping the metal head in position. The metal head holds the base wad in place. A separate base wad may be made of rolled paper, molded composite or molded polyethylene plastic.
- Integral—An integral base wad is part of the tube itself and formed when the tube is manufactured. It is not a separate piece and can never become loose or be pulled into the bore.
Most shotshells have a metal head made of brass, brass-plated steel or brass-plated aluminum. Shotshells that do not have a metal head generally are molded types that have a metal reinforcing disk embedded in the rim. The primary function of the metal head is to reinforce the rim for positive extraction and ejection. Metal shotshell heads are available in different heights, with target loads generally having the lowest and magnum hunting shells the highest (thus the popular terms “low brass” and “high brass”). The height of the metal head serves chiefly to distinguish hunting loads from target loads as shotshells with high metal heads are not stronger than those with lower metal heads.
Rimfire Cases
Rimfire cartridge cases have been in continuous production since the mid-1850s, making this type of self-contained cartridge the oldest in production. In the 1800s, there were many calibers of rimfire ammunition ranging from the humble .22 Short to massive .50-caliber examples. Presently, new .17-caliber rounds have joined traditional .22 cartridges as commercially loaded rimfire offerings.
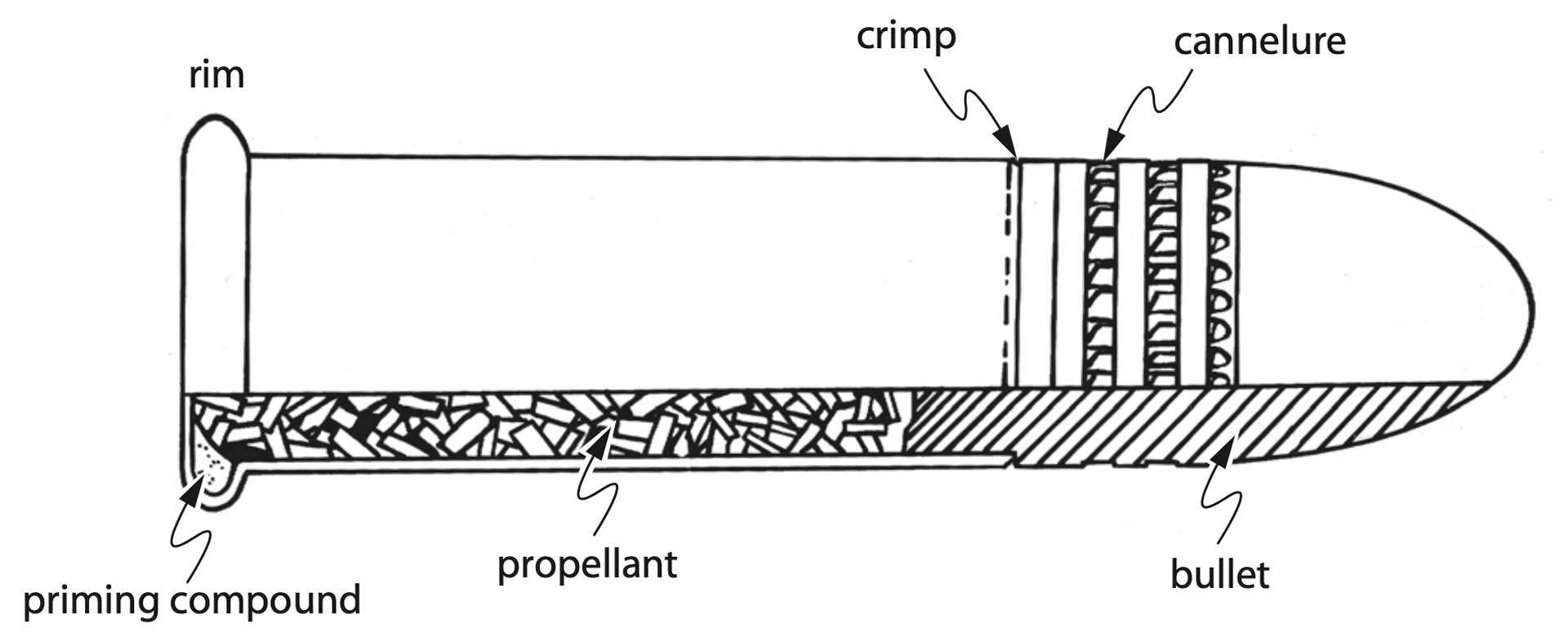
In concept, the rimfire cartridge is elegantly simple. A one-piece cartridge case is drawn from thin brass and formed with a hollow rim. Priming compound is forced into the rim by centrifugal force from spinning. The primed case is then charged with powder and a bullet seated in the case mouth. To provide sufficient bullet push and pull, the bullet is crimped securely into the case mouth. When the firing pin of the rifle strikes the thin brass rim, it crushes the hollow rim
and ignites the priming mixture within. There is no anvil or separate primer cap.
However, the thin brass rimfire case is weak and will not withstand high breech pressures. Ignition is also weak resulting in a very inefficient powder burn. However, the rimfire case is cheap and easy to manufacture. When loaded to moderate breech pressures within its strength limitations, the rimfire cartridge has and continues to provide generations of shooters with low-cost practice, training and small-game hunting capability.
Without ammunition, a firearm is no more than an inefficient club. For this reason, much of the technological development effort in firearms history was devoted to ammunition. Basically, ammunition consists of four parts: powder, projectile, primer and cartridge case. For this article, we will focus on the latter, cartridge cases. Note that the bullet is only one part of a cartridge. Colloquial references to the “number of bullets in a gun” are technically incorrect.