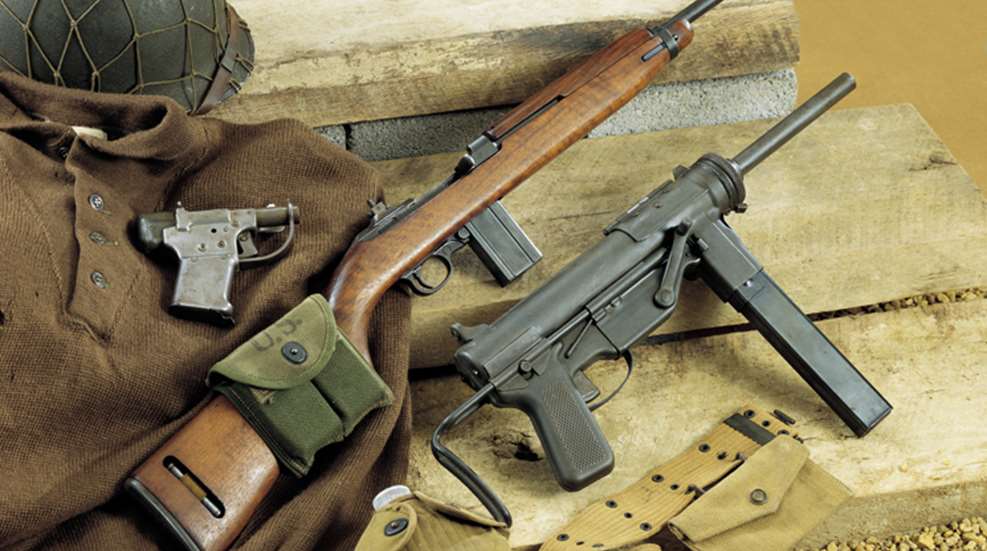
In addition to tanks, trucks, planes and other equipment, GM turned out millions of firearms during the war. The “Liberator” pistol (far l.) and M3 “grease gun” (r.) were made by the Universal Guide Lamp Division while both the Saginaw Steering Gear and Inland Manufacturing divisions made M1 Carbines. M2 .50-cal. machine guns—shown below mounted on a 26th Infantry Division half-track—were made by four General Motors subsidiaries.
This article was first published in American Rifleman, January 2000
World War II represented an unprecedented era in the history of the United States. Never before, or since, has our nation been so focused on a common goal and willing to endure countless sacrifices, large and small, in the life-and-death battle against its foes. Millions of young men and women donned military uniforms and millions more labored in the nation’s factories turning out vast quantities of badly needed war materiel for the Allies. All sorts of businesses from “mom and pop” operations to huge conglomerates producing consumer goods prior to Pearl Harbor were soon overwhelmed with orders for items ranging from uniforms and small arms to aircraft and warships. The staggering amount of war materiel manufactured in the United States from 1941 to 1945 is a tribute to the efforts of American industry under the most trying conditions.

An outstanding example of such manufacturing prowess and versatility during World War II is reflected in the efforts of General Motors Corp., which was, of course, a well-known manufacturer of motor vehicles and related items through a number of different manufacturing subsidiaries. When the U.S. government began to place orders for all manner of arms and equipment in the early 1940s, GM was a logical supplier. It should be no surprise that the firm turned out large numbers of trucks and other vehicles in addition to several types of military aircraft. Nonetheless, it may come as a surprise to some that GM was also a major supplier of firearms to the U.S. military.
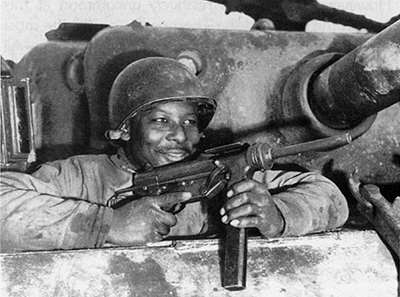
As stated by C.E. Wilson, who was president of GM in the early days of World War II: “I feel we were selected for this important undertaking [firearms production] because our manufacturing of precision automobile parts on a large scale has developed engineering and technical talent that can readily and efficiently be turned to producing such equipment.”
Saginaw Steering Gear Division, Saginaw (and Grand Rapids), MI
Among the first General Motors subsidiaries to become actively involved in manufacturing arms was the Saginaw Steering Gear Division in Saginaw, Mich. Saginaw’s participation in producing military arms actually predated Pearl Harbor by several years with the U.S. M1919A4 light machine gun.
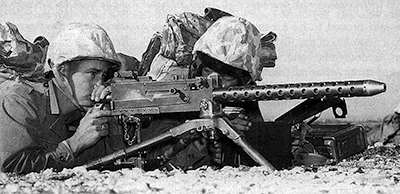
M1919A4 Machine Gun. This .30-cal., air-cooled machine gun was designed to be more portable than the much heavier water-cooled M1917. The basic action was the same as the John Browning-designed .30-’06 Sprg. M1917, but it weighed substantially less since it lacked the water jacket and other equipment required by water-cooling. The heavy M1917 tripod was replaced by a much lighter unit. The M1919A4 weighed 45 lbs. with tripod, which was less than half that of the M1917A1.
Prior to the war, M1919A4 production was quite limited, and a few nearly handmade examples were turned out by the Rock Island Arsenal. It was recognized that production capacity would have to be dramatically increased. In April 1939, the Ordnance Department contracted with Saginaw Steering Gear Division to conduct engineering studies regarding the feasibility of machine gun production. The company’s experience in mass production of machined components having exacting tolerances made it well suited for the production of modern arms. Saginaw’s first M1919A4s began coming off the assembly line in March 1941. Two other firms also made them, but Saginaw, by far, turned out the largest number—389,251 M1919A4s were produced there during World War II.
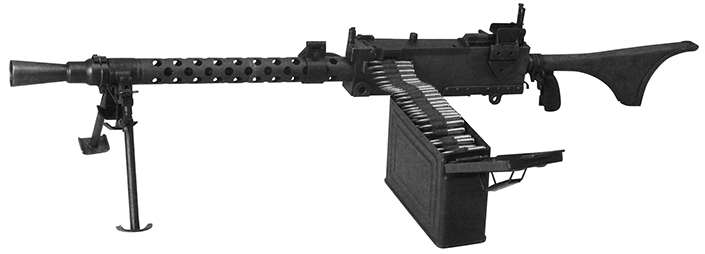
M1919A6 Machine Gun. While the M1919A4 was a definite success on the battlefield, a more portable version was sought by the infantry. The result was the M1919A6. It was essentially a M1919A4 action fitted with a shoulder stock and bipod. Weighing 321⁄2 lbs., it was lighter than the tripod-mounted M1919A4. It was, however, much heavier and bulkier than the Browning Automatic Rifle that it was supposed to replace, but the M1919A6 saw a fair amount of use late in the war. Saginaw turned out 43,479.
M1 Carbine. Saginaw produced large numbers of M1 carbines under government contract during the war. The carbine was developed by Winchester Repeating Arms Co. and was adopted in late 1941. The carbine was designed to be a supplemental arm to replace the handgun for troops too burdened with other duties to effectively carry a standard service rifle. The carbine was a lightweight semi-automatic that fired the .30 Carbine cartridge.
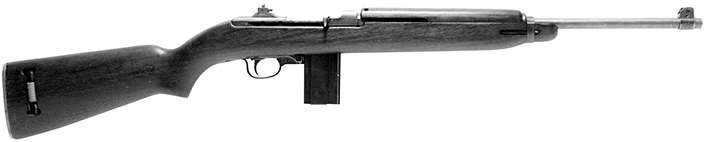
Ten firms received contracts to make carbines, and Saginaw received its first contract in February 1943. Deliveries began in April of the same year. The company was assigned two serial number blocks (3,250,020-3,651,519 and 5,834,619-6,071,188). The name of the maker (“Saginaw SG”) was stamped next to the serial number behind the rear sight. The barrel was also marked “Saginaw S.G. Div./General Motors” behind the front sight. Many components were stamped with “SG.”
Saginaw also took over the contract of the Irwin-Pedersen Arms Co. of Grand Rapids, Mich. Irwin-Pedersen was the only one of the original prime contractors that was unable to successfully deliver on its contract of 112,520 M1 carbines in March 1942. No complete carbines were delivered prior to the demise of the company. In March 1943, the government negotiated with Saginaw to take over. It agreed to do so, and, eventually, carbines were flowing from Saginaw’s Grand Rapids, Mich., plant using many of the components produced by Irwin-Pedersen, including receivers. The Grand Rapids plant was assigned the code marking “S’G’” and virtually all of these carbines had a mixture of Irwin-Pedersen parts (marked “IP”) and “S’G’” parts. Saginaw Steering Gear was the only carbine contractor to operate two separate plants. The combined total of 517,212 M1 carbines from the two plants represented about 8.5 percent of total production. The firm’s managerial, engineering and production prowess were recognized as being among the best of any commercial enterprise during the war.
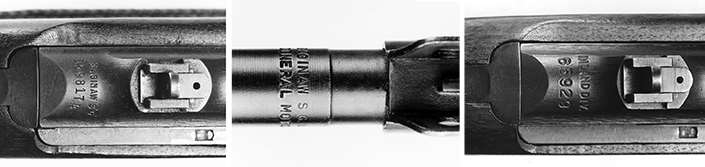
Inland Manufacturing Division, Dayton, OH
Saginaw was not the only GM subsidiary to manufacture carbines during the war. A General Motors affiliate, the Inland Manufacturing Division, produced the largest number of carbines of any manufacturer.
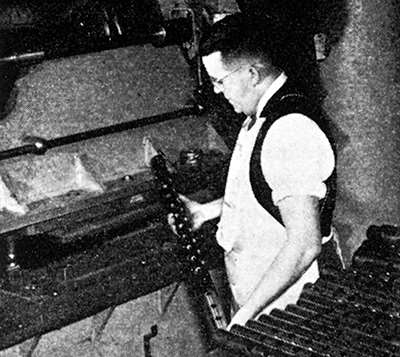
M1 Carbine. Inland worked with designer George Hyde on his “light rifle”—which competed against the Winchester design in the trials—and submachine gun designs. Even though Hyde’s carbine entry was unsuccessful, the Ordnance Department was impressed with Inland’s expertise and talent, and the firm was seen as an ideal manufacturer for the new carbine. Soon after the M1 carbine was adopted, the government worked out a production arrangement with Winchester and Inland to produce the new arm. Winchester’s production capacity was inadequate to meet even the preliminary estimates. Inland had a large and well-managed manufacturing capability and eagerly accepted the challenge. Later, Inland was very helpful in assisting several other carbine prime contractors (including Saginaw Steering Gear) with setting up their carbine production. The first mass-production M1 carbines were flowing from Inland’s assembly line by May 1942.
M1A1, T3 and M2 Carbines. Inland also produced the “M1A1” Carbine, which had a folding stock for airborne use, the “T3” Carbine, which had a specially manufactured receiver designed to mount an infrared night vision sight, and the M2 selective-fire carbine. Inland was the sole producer of the M1A1.
Inland was, by far, the largest manufacturer of carbines during the war: 2,632,097 carbines or 43 percent of the total. Inland and Winchester also stayed in production longer than any of the other prime contractors and made carbines until mid-1945. Inland will always be known as the biggest producer of M1 Carbines during the war, which was a crowning achievement for that GM subsidiary.
Guide Lamp Division, Detroit, MI
The Guide Lamp Division of General Motors had extensive experience and plant capability for mass-production of stamped-metal components. While this would not, at first thought, seem suited for the production of firearms, changes in technology made this type of manufacturing ideally suited to certain types of guns. The time and expense necessary to produce traditional, finely crafted arms was rapidly becoming an unaffordable luxury. Methods to reduce production time and cost were explored, and guns fabricated from inexpensive stamped sheet metal components were seen as the future. The first of this type to see widespread production and use was the British Sten 9 mm submachine gun. While the crude-appearing Sten offended the sensibilities of many traditional-minded military people, its fast production and low cost were too great to ignore, and it was soon adopted by the British.
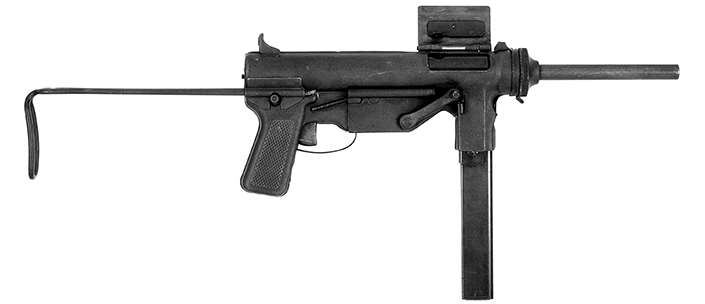
M3 Submachine Gun. The success of the Sten did not go unnoticed. The standard American military submachine gun at the time was the legendary .45 ACP-cal. Thompson, which was produced in large numbers early in the war because no other submachine gun design was then available and ready for production. The Thompson was very costly and time consuming to manufacture. With this in mind, a gun designed by George Hyde was adopted in December 1942 as the “U.S. Submachine Gun, Caliber .45, M3.” The M3 was fabricated largely from stamped and welded sheet metal. It fired the same .45 ACP cartridge as the Thompson and M1911A1 pistol. It was not capable of semi-automatic operation, but was designed with a low cyclical rate of fire of 450 rounds per minute, enabling an experienced shooter to squeeze off single rounds. The M3 used a 30-round, detachable box magazine. Because of the almost uncanny resemblance to the automobile mechanic’s tool, the M3 soon gained the nickname “grease gun.” The M3 had a sliding wire stock that could be retracted.
Due to the nature of the M3’s design, Guide Lamp was the logical firm to make it. Guide Lamp began M3 production in the summer of 1943, and the gun began to see issue by the fall. The M3 was not widely popular, and many combat troops complained about having to exchange their trusted Thompsons for “grease guns.” Nevertheless, as the war progressed, larger and larger numbers of M3s were issued. Its compact size was popular with paratroopers, tank crewmen and other specialized troops. Guide Lamp produced 605,664 M3s.
M3A1 Submachine Gun. While the M3 had a number of desirable attributes, some problems were encountered which necessitated a redesign. In December 1944 the “M3A1” was adopted. The most distinguishable difference between the two was the elimination of the cocking handle of the M3. The M3A1 was cocked by simply inserting a finger in a recess of the bolt and pulling it back. Other changes included an enlarged ejection port, a protective guard on the magazine release and strengthening of internal parts. Guide Lamp produced 15,469 M3A1s until production ceased with the end of World War II. Guide Lamp was the only manufacturer of the M3 and M3A1 during World War II. Some “grease guns” remain in limited use today by the U.S. military, primarily tank crews due to the compact design.
“Liberator” Pistol. If the M3 was an unconventional design, Guide Lamp produced another during World War II that could be characterized as bizarre. It was a single-shot handgun designed to be manufactured very quickly and cheaply for clandestine use in occupied countries. Dubbed the “Liberator,” it was designed at the request of the Office of Strategic Services. It was made primarily of stamped sheet metal and was chambered for the .45 ACP cartridge. The barrel was smooth-bore and the breech-block was hand-operated. After firing, a wooden dowel was used to manually push the fired cartridge case out of the chamber. The pistol was packaged in a wax-impregnated cardboard box holding extra ammunition, a wooden dowel and a comic-strip type set of operating instructions. The latter was utilized so that no language barriers would be encountered by anyone learning to use the it. Five extra cartridges could be stowed inside the grip of the pistol. The intended purpose was to enable indigenous, friendly personnel in enemy occupied territory to receive the Liberator pistols via air-drop or other means and use the Liberator to dispatch enemy soldiers. The partisans could then take the enemy’s more effective gun for subsequent use. Few details regarding actual field use of the Liberator pistol are known. It has been stated, without documentation or definitive proof, that more enemy soldiers were killed with them than with the M1911A1. Approximately 1,000,000 were produced by Guide Lamp between June and August of 1942. The cost was only a few dollars each. The gun weighed about 1 lb. (unloaded), the barrel was almost 4" long and the overall length was about 51⁄2".
Even though large numbers of Liberators were made, relatively few have survived. They were designed to be essentially disposable, which was not conducive to a high survival rate. The high production rate and very low cost are a tribute to the manufacturing prowess of Guide Lamp.
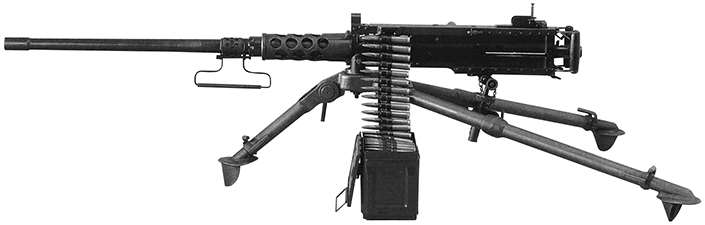
M2 .50-Cal. Machine Gun. On the other end of the small-arms spectrum is the massive and powerful .50-cal. (.50 BMG) Browning machine gun. Details regarding this important arm are discussed in the next section covering the AC Spark Plug Division of GM. There were actually four General Motors subsidiaries that produced the M2 .50-cal. machine gun during World War II. Despite its production efforts on the M3 submachine gun, Guide Lamp was, nevertheless, able to turn out a fair number of the finely crafted M2s as well. This is ample evidence that the firm’s manufacturing talents were not confined exclusively to stamping.
AC Spark Plug Division, Flint, MI
The AC Spark Plug Division of General Motors produced practically all of the spark plugs and other automotive ignition products for the corporation. Just prior to the U.S. declaration of war, AC Spark Plug, along with several other GM plants, began plans to produce arms.
M2 .50-Cal. Machine Gun. One of those that was needed in very large numbers was the .50-cal. Browning M2 machine gun. The M2 was not only utilized as an infantry and anti-aircraft arm, but was also the standard machine gun for most U.S., and some British, aircraft. Most U.S. fighters mounted from six to eight of them, and heavy bombers such as the B17 and B24 had more than a dozen. The very large number of military aircraft produced obviously meant that great numbers would be needed. A total of 1,964,418 Browning .50 cals. of all types were made during World War II. Eight different manufacturers produced the gun during the war, and half of them were General Motors subsidiaries. The largest manufacturer of the M2 was the AC Spark Plug Division. The company manufactured the three major variants: the air-cooled aircraft gun (61 lbs.), the water-cooled anti-aircraft gun (1211⁄2 lbs.) and the air-cooled “tank and field” model (81 lbs.). The latter type was primarily an infantry arm and was often mounted on a tripod for field use. The rate of fire ranged between 450 and 575 rounds per minute (depending on the model) and normally fed from a metallic-link belt with 110 rounds per belt. Very early examples had a 36" barrel but virtually all manufactured during the war were fitted with 45" barrels to improve ballistic performance. Of the nearly 2 million M2s produced, 347,524 of were the infantry version.
Its extremely widespread use on aircraft, ships and by the infantry is a tribute to the versatility of John Browning’s heavy machine gun. As stated during the war by Brig. Gen. James Kirk, Chief of the Small Arms Branch of the Ordnance Department Industrial Division: “This gun is one of the few weapons used by all our armed services alike. In addition to its employment as an aircraft gun by the Army Air Forces, the caliber .50 is used by the Ground Forces as an antiaircraft-antipersonnel weapon and, with armor-piercing ammunition, against light tanks and armored cars.” The M2 was one of the premier military arms of all time and the basic design remains in use today.
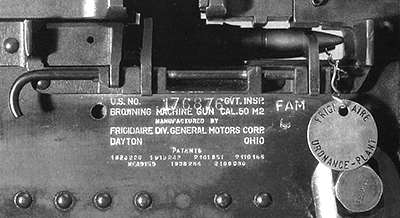
Frigidaire Division, Dayton, OH
Along with the AC Spark Plug Division, General Motors’ Frigidaire Division was one of the prime manufacturers of the M2. Frigidaire was well-known before the war as a major producer of refrigerators, freezers and other consumer appliances.
M2 .50-Cal. Machine Gun. The firm was not only a major manufacturer of the M2, but its engineering department was also instrumental in modifying and redesigning certain components to either increase production rates or reduce costs. Frigidaire was the developer of the “T26” .50-cal. machine gun, which was essentially an M2 modified for a higher cyclical rate of fire. The T26 concept was not adopted due, in part, to interchangeability problems, and further development was not forthcoming. Frigidaire’s ability to switch from producing such experimental arms to efficient mass-production of the M2 is yet another example of the outstanding managerial and labor prowess of American industry.
Brown-Lipe-Chapin Plant, Syracuse, NY
M2 .50-Cal. Machine Gun. The Brown-Lipe-Chapin plant at Syracuse was a rather unheralded producer of war materiel including M2s. In addition to producing the M2, Brown-Lipe-Chapin also manufactured many ancillary items for other arms including barrels for M1 carbines and other types of replacement components. The firm remains a little-known but important supplier of military armaments to the United States during the war.
While the contributions of American industry to the war effort are well-known, General Motors’ production of firearms may not be widely known to many people today. Most are not surprised that the corporation turned out trucks and other types of vehicles, but many are not aware that GM was also a major supplier of carbines, submachine guns and machine guns to the U.S. government during the war. The efforts of General Motors and many other American corporations were a major factor in allowing the Allies to defeat the forces of oppression during World War II.