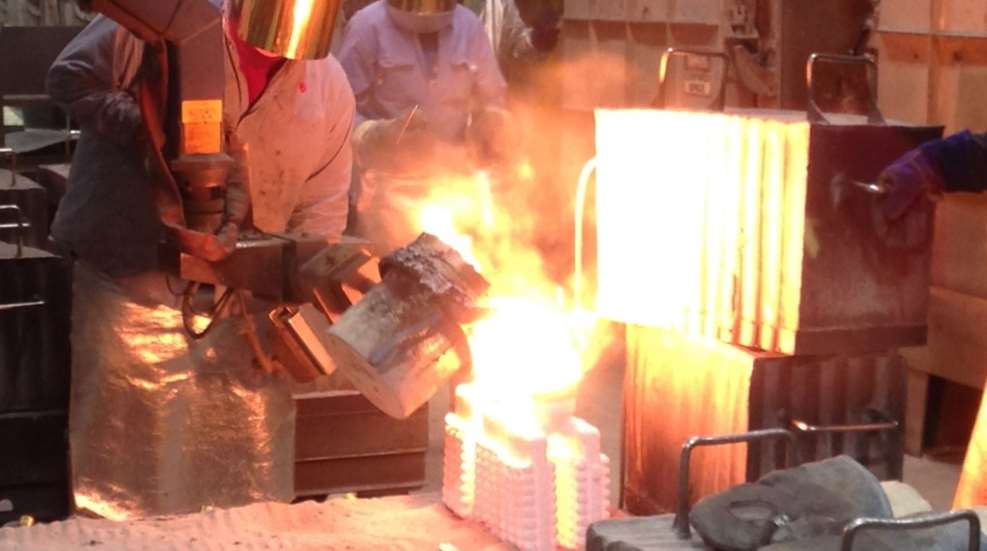
With the predominance of highly accurate CNC machines throughout the firearm industry, techniques such as forging and casting tend to seem a bit outdated and lacking precision. Whether it's a huge forge at Smith & Wesson—rhythmically pounding hot metal with a giant hammer—or Ruger’s foundry with its molten steel, these dramatic operations do seem a bit primeval. The reality, though, is quite the opposite.
Investment casting, sometimes called “lost wax” casting, is a manufacturing technique that dates back nearly 6,000 years. Ancient Egyptians used it to create jewelry and ornaments, and the method has been in continuous use throughout recorded history. As technology has advanced, investment casting has improved, and the computer-aided process employed by Ruger in the manufacture of its firearms is precise and efficient. Here is a brief look at the Newport, N.H.-based firm’s modern take on ancient tech.
The Mold
It all starts out with small, blue wax pellets. Fed into a machine and molded according to digital blueprints, the pellets form positive impressions of whatever metallic component is being cast. Want to make a slide handle for a Mini-14? Start off with a waxy blue model. Once several molds are produced, 14 in the case of the handles, they are attached to a central tree or runner, also made of wax. This is done by melting a bit of wax at the attachment point of both the model and the tree—using, essentially, a hot butter knife—and then sticking the parts together. Though the models are highly accurate copies of the end components, extra material is strategically added to facilitate attachment and, later, separation from the runner without damage to the component itself.
Once the models are melded to the tree, the entire fixture is dunked into a solution of citric acid for cleaning and to make the wax tacky. Once treated, the tree is cycled through a cement-like slurry, a vat of fine sand and drying racks. Coat after coat, the slurry forms a shell around the tree and the fine sand penetrates into all the interior nooks and cavities.
When the shell is sufficiently thick and thoroughly dried, the tree is taken to a furnace for de-waxing. As the shell is heated the wax begins to melt and drain out. Once complete, all of the wax has melted or been burned out of the shell, leaving only a hollow mold. Most of the melted wax—about 75 percent—is recovered and re-molded into runners. The other 25 percent is why the process is known as “lost wax” casting.
The Metal
Once the mold, or shell, is complete, all that remains is to refill it with molten metal. To do this, the shell is again heated—filling a cold shell with hot metal would cause cracks and breaks. Likewise, the requisite metal, let’s say steel, is melted. At this stage, Ruger often combines recycled and virgin metal for its castings. When ready, the liquefied metal is poured into the heated molds, filling all the spaces left from the wax and creating a lively shower of sparks and flame in the process. The filled molds are immediately covered in air-tight boxes to help prevent pollution or impurities in the metal, and the cooling process begins.
After the metal has cooled and hardened, machines shake and blast the shell off of the components. Next, the individual components are cut from the now-metal central tree, and are treated in acid and alkaline solutions to remove any remaining shell, especially from internal recesses. Components are then heat-treated for hardness, and any finishing work is conducted—either by hand or in a CNC station—to bring the components to specification. It should be mentioned that the raw cast parts actually require very little finishing work, at least compared to my preconception; the accuracy and detail achieved by the molds is outstanding.
While not the most glamorous or modern technique, companies such as Ruger are proving every day why investment casting techniques are still relied upon in firearm manufacture. The practice has been around for thousands of years and, if the folks in Newport have any say, they’ll be using it for a while longer.