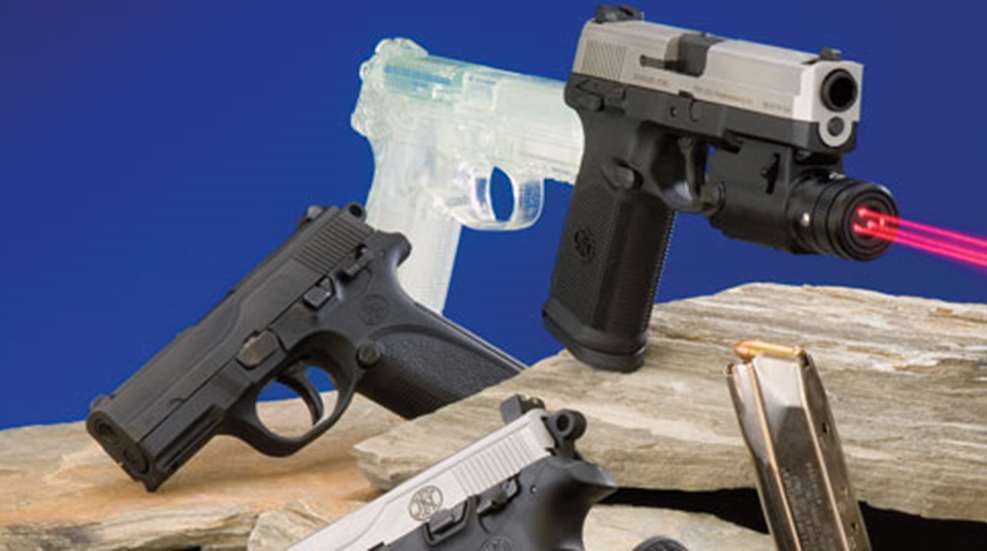
Since the end of the 19th century, Belgium’s Fabrique Nationale has relied on the performance and commercial appeal of Browning pistol designs, starting with the Model 1899 and including the renowned Hi Power. When FN undertook the development of a line of polymer-frame pistols at the dawn of the 21st century, the company decided to develop and produce them entirely at its American facility, which is dedicated primarily to the production of U.S. military rifles and machine guns, and to Winchester Model 70 and FN SPR bolt-action rifles.
The pistols were to be of a new design and compliant with both U.S. and international safety standards to enable worldwide sales to militaries and law-enforcement agencies. Design, engineering and production were assigned to FN Manufacturing, Inc. (FNMI) in Columbia, S.C., while sales, distribution and training courses were to be handled by FNH USA in McLean, Va.
The first FNP pistol, the FNP-9 (9 mm Luger), appeared in 2001, but large-scale distribution was delayed until 2003. Other models, including the FNP-40 (.40 S&W), FNP-357 (.357 SIG) and FNP-45 (.45 ACP) followed. On average, FNP pistol designs go through a three-year development cycle. Although the FNP-9, FNP-40 and FNP-357 are variants of the same design concept, the FNP-45 was made to comply with U.S. military specifications. When developing the FNP-45, the design and engineering team worked at further improving ergonomics, trigger pull weight and reset, and sights—the latter for faster target acquisition. Additionally, the FNP-45 was made completely ambidextrous. Like the other FNP pistols, the FNP-45 had a serviceable frame with replaceable stainless steel rails on which the slide rode. That characteristic was a requirement from the pistol’s inception and remains a distinguishing feature.
The FNP-9, FNP-40 and FNP-357 went through an endurance test of 20,000 rounds. The FNP-45’s endurance test requirement was raised to 25,000 rounds. Any design modification automatically triggers an additional 10,000-round endurance test. The standard Sporting Arms and Ammunition Manufacturers’ Institute (SAAMI) test requires a drop test from 5 feet in “safe” mode on a rubber mat. FNMI takes this a step further: FNP pistols are dropped from 5 feet in “cocked” positions onto a concrete floor. Other abuse tests include mallet strikes attempting to force hammers to drop and firing with plugged barrels.
Thermal testing is conducted from 40 degrees below zero to 140 degrees F in compliance with military requirements. Each model has to function without problems throughout this temperature range. Olivier Coulombier, the engineering product manager, explained that in the year the FNP-45 pistol was introduced his staff fired 200,000 rounds to detect potential issues and guarantee reliability. A separate indoor test-firing range was built away from the production test range next to the R&D department, and it includes an adjacent tool room for prototypes to be worked on.
As many as a dozen engineers were assigned to FNP development at any one time, and the current research and development staff for the FNP stands at five engineers. The engineers view the pistol as a system, comprised of different modules, each with dedicated engineering support. The modules are interrelated, and include the slide module, the trigger-group module, the rails module and the fire-control module.
In addition to Computer Assisted Design (CAD) software, the engineers use Adams 3D interactive software, which was adapted from the automotive industry for product development. The software simulates all phases of functioning and firing and allows the engineers to see how parts and modules operate together so that problems can be identified prior to production.
The first prototype stage includes a synthetic model made through Fused Deposition Modeling (FDM), a rapid 3D prototyping method. Unlike sculpted models or formed models made from molds, the FDM system creates a synthetic prototype based directly on the computer model. This allows the engineers to create an accurate model of their design in a few hours. The synthetic prototype is used to evaluate ergonomics and handling in general.
Once the FDM prototype is approved and the engineers work out the virtual mechanical functioning, the first prototype is built. Unlike the traditional, time-consuming and labor-intensive steel machining and milling, FNMI uses Metal Laser-Sintering (MLS). This highly advanced laser system is used to create complex metal parts for functioning prototypes. It reduces the time from design to prototype and is more cost-effective.
The use of three-dimensional interactive software, FDM prototypes and MLS allows FNMI to quickly and cost-effectively create functioning prototypes reflecting each engineering change during development, a capability that many manufacturers do not have.
Production and assembly of the FNPs is done at FNMI, and all components are manufactured in the United States. The pistols are offered in a number of finishes: Slides are available in matte black, polished stainless and flat-dark earth. The polymer frame is either matte black or flat-dark earth. All slides, even those that are coated, are made of stainless steel to enhance corrosion resistance. The matte black and flat-dark earth finishes are applied using Physical Vapor Deposition (PVD), a gas application in a vacuum chamber. Unlike the traditional Melonite finishing, which is a heat-treatment process, PVD coatings do not affect the metallurgy of the steel and have superior wear characteristics.
Barrels are hammer-forged by FNMI using the same techniques used to manufacture M240 and M249 machine gun barrels. Magazines are stainless steel and hold up to 16 rounds for the FNP-9, and 14 for the FNP-357, FNP-40 and FNP-45. A special one-round extension magazine is available for the FNP-45, increasing its capacity to 15.
Each pistol is hand-assembled by a small team of dedicated FNMI employees. Assemblers look for fit and finish, and perform initial testing. The pistol assembly department is small and is located above the M240 and M249 machine gun assembly stations. Because FNMI is a large U.S. military supplier, employees are conscious of the fact that the lives of U.S. servicemen depend on their products. The same care and attention that goes into the manufacture of M240 machine guns goes into the production of each FNP pistol.
Each production pistol goes through a function test, feed test and a factory proof test in which one high-pressure round is fired. Barrels are final-proofed and marked. Additional tests include test firing with standard ammunition, accuracy testing (3-inch maximum group at 50 feet) and targeting testing (five shots centered within a 6-inch circle centered 1.5 inches above aim at 50 feet). Completed pistols are packaged in a hard case and shipped with a total of three magazines and two interchangeable backstraps.
There are no operational or testing differences between pistols that are destined for the commercial market and those intended for the military or law enforcement. Although the mechanics are identical, there are some cosmetic differences. Currently the commercial FNP-45 has a more rounded top to the slide while the military version is flat. This was done to improve the aesthetics of the commercial model. The military model also has front slide serrations, which are absent on the commercial model. Military pistols also currently feature more aggressive checkering than that of the commercial pistols.
Special features are available or can be developed for military and law enforcement customers. Pistols can be modified to accept suppressors, and FNH USA sells a variety of extended threaded barrels with different threads and pitches. These modified pistols for suppressed firing are equipped with raised sights to provide a line of sight that clears the suppressor body. Night sights are available as an option for both standard and raised sights.
Recently the engineering staff developed an FNP-45 model with an integrated Trijicon red-dot sight. This was a joint development between FNMI and Trijicon, and the unit mounts on top of the slide, which is milled to accommodate the base of the sight. The sight operates for 5,000 hours without the need to replace batteries. It was extensively tested at FNMI; 5,000 rounds were fired without any failures of either pistol or sight. The sight is mounted so as to permit use of the iron sights as a backup.
I was fortunate enough to fire one of the latest prototypes, a select-fire FNP-9 pistol. The model does not yet have a formal designation, and it is unknown if any production pistols will be made. In full-automatic firing the pistol was surprisingly manageable. Even with its high rate of fire, it proved to be reliable and very controllable with just minor practice. Although the select-fire pistol has some unique features, the basics of the pistol remain identical to production pistols—this attests to the strength and reliability of the FNP design.
Military and law-enforcement pistols are built to order, and the company gladly accepts special requests. Numerous U.S. law enforcement agencies use FNPs, and they have been adopted in Spain, the Dominican Republic, and Middle Eastern countries among others.
FNH USA has always been community-minded. When it learned that South Carolina had budget problems to acquire new handguns for its Dept. of Corrections, the company stepped up and donated the pistols. The FNP line proves that reliable, quality products can be built in the U.S. without compromising features or affordability.